ONSHORING & RESHORING
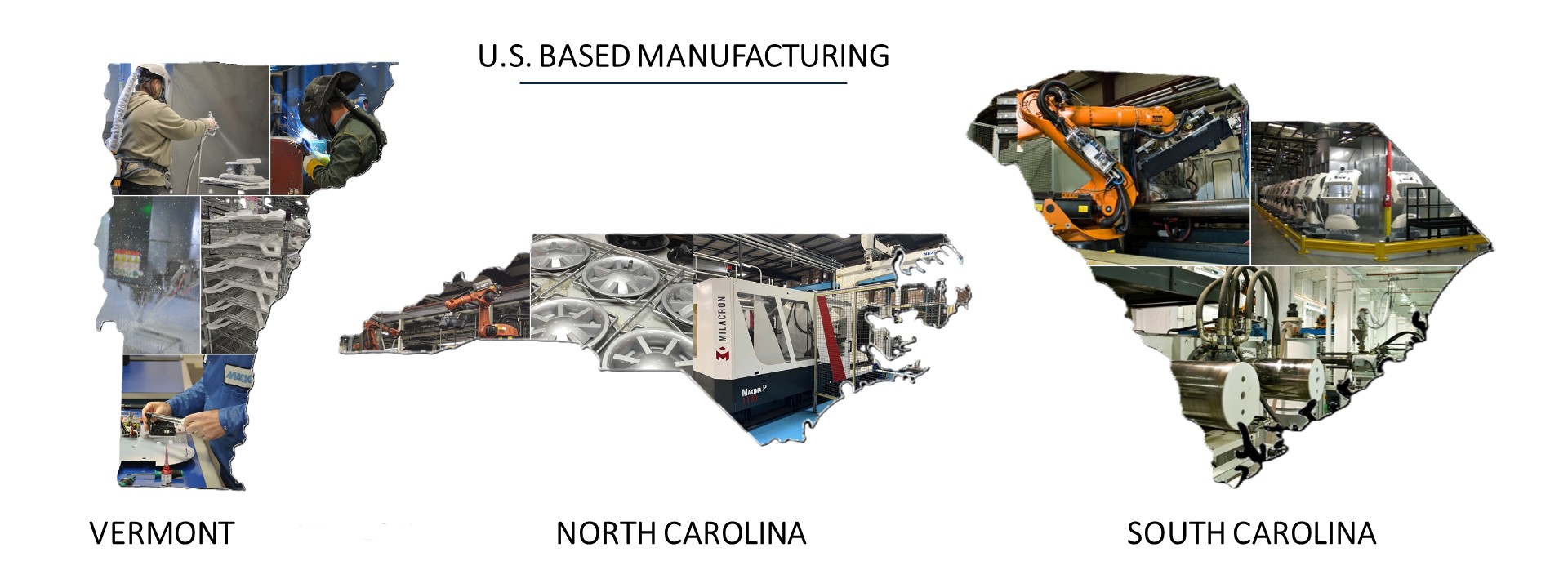
Strategic Locations for Onshoring Success: Mack Molding’s Facilities Positioned to Support Domestic Manufacturing and Supply Chain Resilience
Onshore & Reshore with Confidence – Mack Molding is Your U.S. Manufacturing Partner
The Case for Onshoring & Reshoring
Rising tariffs, global disruptions, and increasing costs have made reshoring to the U.S. more strategic than ever. The true cost of offshore manufacturing—including shipping, travel, IP risks, and supply chain instability—was never fully vetted. Now, with supplier costs rising and quality concerns growing, the once-attractive savings of offshore production are diminishing.
A well-documented, reliable U.S. supply chain reduces risk, ensures quality from the start, and delivers long-term cost savings. Companies that act now gain a competitive edge with a cost-effective, high-quality, and resilient domestic manufacturing strategy.
Challenges Companies Face When Reshoring
Reshoring isn’t as simple as moving from Point A to Point B—it requires overcoming key obstacles:
- Lack of CAD Models & Engineering Data – Offshore manufacturers often withhold design files.
- Missing BOMs & Work Instructions – Many companies must recreate production documentation from scratch.
- Component Substitutions – Offshore suppliers swap parts frequently, requiring software updates and revalidation to ensure consistency and compliance.
- Intellectual Property Risks – Offshore manufacturing can compromise proprietary designs competitive advantage.
- Quality & Communication Gaps – Poor quality, communication, and documentation can drive up costs significantly—especially when issues are discovered too late. If a defective product is already on the ocean, the damage is done, leading to delays, rework, and lost revenue.
- Lost Institutional Knowledge – Relying on offshore partners often erodes internal expertise on parts and assembly, making transitions and troubleshooting more challenging.
- Uncertain Costs & Lead Times – While reshoring has upfront costs, long-term savings and stability outweigh them.
- Retooling & Sourcing Challenges – Many companies discover they don’t own their molds and tools, requiring careful planning.
Proven Experience in Onshoring: Mack Molding’s Expertise in Rapid, Scalable Transitions
At Mack Molding, we understand these challenges and provide end-to-end solutions for a smooth transition. We have successfully onshored manufacturing for a variety of products, including agricultural components and commercial appliances. Our approach to onshoring is the same as any other Mack Molding job—it receives our full attention and commitment to execution.
The Process
The process begins with a thorough understanding of the customer’s needs, timelines, and existing safety stock to ensure a seamless transition into full production. We establish qualification activities, define acceptance criteria, and build a tailored production schedule to meet customer expectations. In most cases, retooling is required for plastic injection molding jobs to optimize the process for efficiency and quality. For contract manufacturing (CM) work, we focus on de-risking the supply chain by securing domestic or alternative suppliers for critical components such as motors and displays.
Experience with Onshoring
A recent onshoring project involved transferring the production of plastic housings for power electronics and internal chassis for energy storage systems. The move was driven by the need to increase U.S.-made content for regulatory benefits and to mitigate the impact of potential trade policy changes. The project involved transferring multiple tools, including high-volume multi-cavity molds and a complex chassis mold requiring precision insert over-molding and secondary operations.
Investing in Client Success
Mack Molding made significant investments to support the transition, including two new injection molding presses, along with high-temperature TCU’s, sequential valve gate controllers, hot runner controls, material dryers, and robotic automation—totaling over $630,000 in capital expenditures. This investment enabled us to rapidly scale production across multiple facilities, with ten transferred tools running on ten machines, including six 310-390T presses, three 500-580T presses, and one 1500T press. These machines were utilized at full or near-full capacity, ensuring high efficiency and redundancy across operations.
Fast Turnaround for Onshoring
Our aggressive timeline—tool receipt to production approval in just 4-8 weeks per phase—required extensive coordination, including tool modifications, multiple sampling rounds, first article inspections, and capability analysis. Forecasted volumes include 4 million units annually for both lids and bases, with an additional 60,000-80,000 chassis per year. Challenges such as engineering-grade resins with flame retardants, multi-cavity tooling, and complex secondary operations were overcome through Mack Molding’s expertise in high-precision molding and automation. Our strong supplier relationships ensured a steady resin supply, preventing line-down events, while our cross-functional team’s seamless execution and continuous communication with stakeholders enabled a smooth transition. Ultimately, Mack Molding’s financial stability, risk-mitigation strategies, and operational agility reinforced our ability to deliver onshoring projects with speed, efficiency, and precision.
Why Reshore with Mack Molding?
- Tariff-Free U.S. Manufacturing – Eliminate cost instability and supply chain risks.
- Shorter Lead Times – Faster production cycles, on-time delivery, and lower logistics costs.
- Full-Service Contract Manufacturing – From injection molding to assembly, we handle everything.
- Geographic Proximity – Easier collaboration and domestic shipping mean cost savings.
- Industry-Leading Certifications – ISO 13485, ISO 9001, ISO 14001, ITAF 16949 certifications and UL, ITAR and FDA registrations for the highest quality standards.
Our Services: A One-Stop Manufacturing Solution
- Design & Prototyping – Reverse engineering, documentation recreation, and process validation.
- Plastic Injection Molding – Precision, high-quality custom-molded components for a range of industries, including medical, industrial, robotics, commercial, and transportation.
- Machining & Sheet Metal Fabrication – Custom-machined parts and precision sheet metal components for seamless integration.
- Electronics & Mechanical Assembly – Complete, integrated product assembly under one roof.
- Secondary Operations – Ultrasonic welding, painting, pad printing, and more.
- Supply Chain Optimization – Flexible solutions for component sourcing and production scaling.
Mack Molding is ready to help you navigate today’s complex manufacturing environment. Whether you’re looking to avoid tariffs, reduce lead times, or gain greater control over your production, our U.S.-based solutions are the answer.
CONTACT US TODAY TO START YOUR RESHORING PROGRAM!